Since its early stages in 1960, and then conceived as a “solution in the search for a problem”, the development of laser technology and its applications in various sectors, production fields and disciplines has not ceased to evolve.
In our daily life, laser use is embodied in common areas such as barcode reading, document printing, or internet access, but this technique is also useful in various areas of health science, such as the state of myopia interventions or dermatological treatments.
The industrial world was not unaware of the benefit of lasers, which have become an important tool for measuring, examining, monitoring, or treating materials. Since its introduction into the industry in the 1980s and 1990s to date, the development of new sources of laser radiation, such as fiber technology, and the significant increase in peak forces and energies, has led to a new generation of high-performance laser devices. Added to this is the significant cost reduction of these systems, which allows their widespread use. A case of particular importance is the diode laser, which we are talking about in Moore’s Law, in increasing its power and reducing its costs.
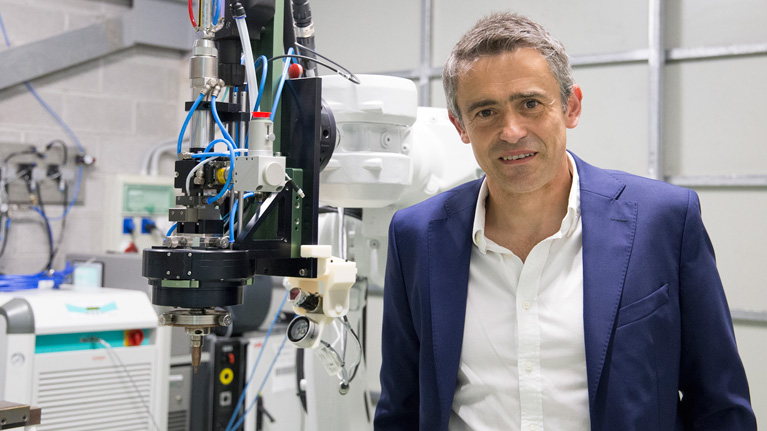
For all these factors, lasers are currently one of the major enabling technologies in the industry and contribute significantly to the development of the so-called Fourth Industrial Revolution or Industry 4.0. On the one hand, it is expected to replace certain traditional processes with others using laser technology, while on the other hand, the use of lasers leads to the emergence of new production processes, among which the additional metal fabrication is the best example.
Laser Technology More efficient, flexible and productive industrial processes
Laser technology-based production operations clearly respond to the requirements suggested by the so-called industry 4.0 in terms of allocation and flexibility in production, reducing life cycles, increasing productivity or improving sustainability.
Lasers are easily digitizable, above all, because of their ability to control their basic parameters (speed, size, beam shape, and energy for each pulse and force). This means that the same laser source can be used to develop various processes such as cutting, welding, or cladding. In addition, the inherent characteristics of this technology provide it with excellent adaptability, which allows not only to quickly modify designs, but also to customize different products in one process.
It should also be noted that the increase in the average forces that can be achieved by current lasers, along with the development of beam processing techniques (multiplication, transformation, and shaping), allow for ever-increasing productivity and make it possible to manufacture complex structures that, until now, had not been It can be achieved profitably.
A clear example is the precise drilling of large areas of aviation applications, where high drilling speeds can make the development of hybrid laminar flow control structures (HLFCs) applicable. Finally, the use of lasers is also an excellent tool for measuring and calibrating machines or end parts, and for monitoring and inspection during the process itself, because it is a technology that does not require communication. In this sense, for example, modern multi-standard interference technologies allow automatic verification of machine tool engineering at all volumes of work in short periods of time and barely interfering with people.
Added manufacturing and 3D printing of metal materials
The development of added manufacturing technology is the basis of what is called Industry 4.0, as it contributes to obtaining components faster, more flexible and accurate in some areas of application. However, these technologies were used primarily to obtain plastic prototypes, which is why additional manufacturing is repeatedly linked to the concept of rapid prototypes. Extending these operations to true advanced manufacturing cases requires, in many cases, the use of materials with good mechanical and thermal properties, and, accordingly, it is necessary to use mineral materials. Thus, obtaining metal parts is an important milestone for carrying out additional manufacturing in production processes.
Today’s laser technology provides two main methods for manufacturing added metals: Selective Laser Manufacturing (SLM) and Direct Laser Deposition (LMD).
In the first case, the piece is created layer by layer on a layer of metal material in the form of a powder. The final quality of the piece is determined by the thickness of each fabricated layer (in general, in the order of tens of microns), by parameters and by the quality of the laser used for fusion.
The main advantage of LMD technology is that it allows additional fabrication on surfaces with sophisticated engineering and, ultimately, on prefabricated parts using other technologies. Moreover, the volume of manufactured parts is limited only to the range of movement of the machine, which makes it possible to manufacture large parts (> 1 m 3) with high precipitation rates (> 2 kg / h). Generally speaking, this type of manufacturing requires final treatment in the case of applications that define a good surface finishing.
In cases requiring a good final finish, LMD fabrication includes post-treatment of surface cutters that require little effort either in time or in difficulty.
LMD: injection by powder and by metallic wire
Today, LMD technologies coexist by injecting powder and strings on an industrial scale and each one is applied in different situations. In the event of dust, it is a process with greater cultivation and technological development due to less difficulty and greater availability of materials. This makes it widely used in reinforcement and repair operations.
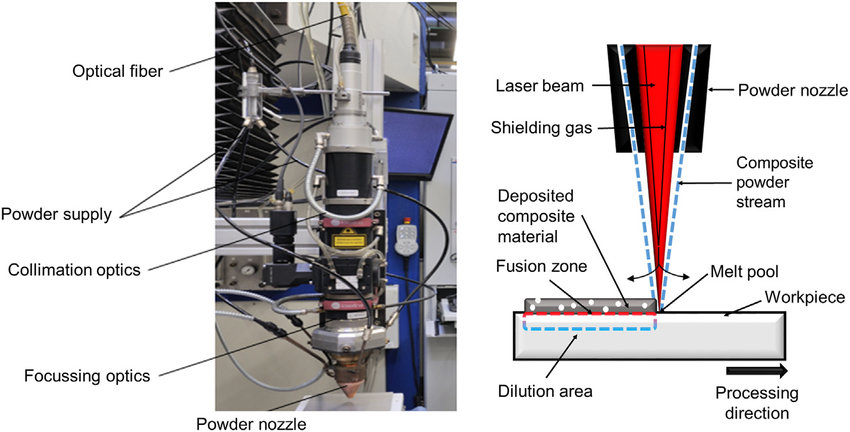
However, recent developments in the design of heads and wireframe materials provide advantages such as the loss of deposited materials approximately near zero, a faster precipitation rate, greater ability to adapt to manufacturing methods added to hybrid parts and a more environmentally friendly work, among other benefits.
The importance of process control
The importance of controlling these manufacturing processes, which clearly defines the structural and mechanical properties of the finished parts, must also be noted. Likewise, a deep description (structural, chemical, mechanical, etc.) is required throughout the entire process, from the base materials to the last part. There is no doubt that these aspects are of unique importance for certification and acceptance of products manufactured using these technologies.
In addition to the above considerations regarding laser-based manufacturing processes, there is an important current trend that focuses on the design and manufacture of resources, components, and equipment that allow for the emergence of faster, more reliable, and more secure operations. This area covers the emergence of new designs and the development of small components for the manufacture of complex equipment.
As a general conclusion, the current state of laser technology means that it should be considered a major carrier in the development of advanced manufacturing processes required by Industry 4.0 and is a clear complement to traditional processes (cutting, welding, cutting, heat treatment, etc.). Moreover, this technology also favors the emergence of new manufacturing processes in the field of manufacturing added metals.
Lasers Manufacturing Lab
No stranger to this trend, as a result of nearly 20 years’ track in developing laser technology and responding to new demands, IK4-Tekniker has established a laser manufacturing lab, which offers global solutions based on specialized and comprehensive knowledge of laser technology and its application from an integrated perspective to advanced manufacturing: processes Manufacturing – specialized in LMD for each wire -; design and manufacture of equipment and components; manufacturing, inspection and additional measurement.
Lasers for manufacturing is a way to reach more and better industry and solve the specific needs of advanced production through the capabilities offered by laser technology, because it provides a 360-degree view of this technology and its application. It also ensures, thanks to his knowledge and equipment, comprehensive control over the process, including the structural and mechanical properties of the final parts.